Quality management
Our focus is on Total Quality Management principles. All of our operations are in line with the DIN EN ISO 9001 and DIN EN ISO 13485 standards and the applicable normative, legal and regulatory requirements.
For us, quality assurance is not just a business area, but a duty of all employees. The Computer Aided Quality (CAQ) system is networked across all locations and available at all times.
The management processes are documented and regulated in an Integrated Management System (IMS). The exact core contents are described in the Integrated Management Handbook (IMH).
In order to meet our customers' requirements, our company is controlled by a central, fully integrated management system. It includes all operational divisions and is available at all times via a location-wide structure.
Work hygiene is an essential component of our production process – especially in clean rooms. The effectiveness of the hygiene requirements is monitored and documented with regular controls of the particle count in the ambient air and microbiological analyses in accordance with GMP guidelines.
Your contact person
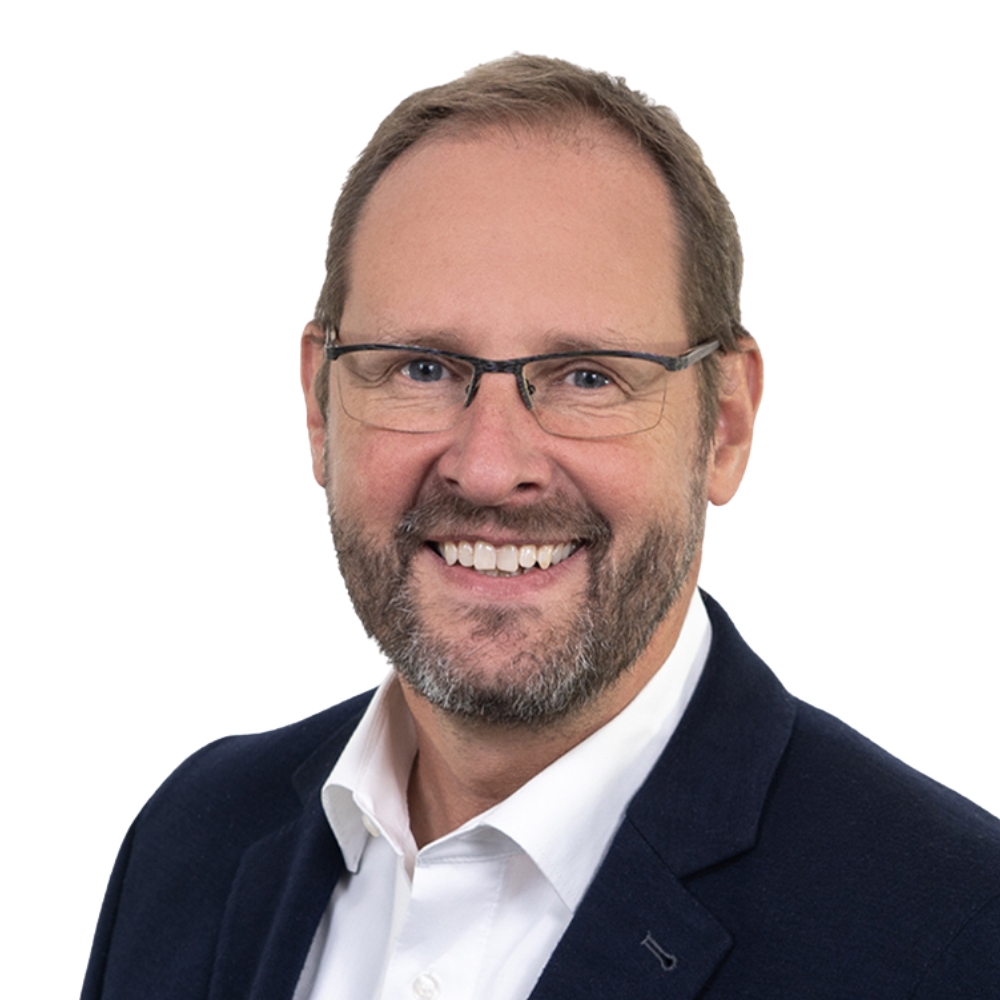
Johannes Weiglein
Quality Management
Representative (QMR)
Quality assurance principles
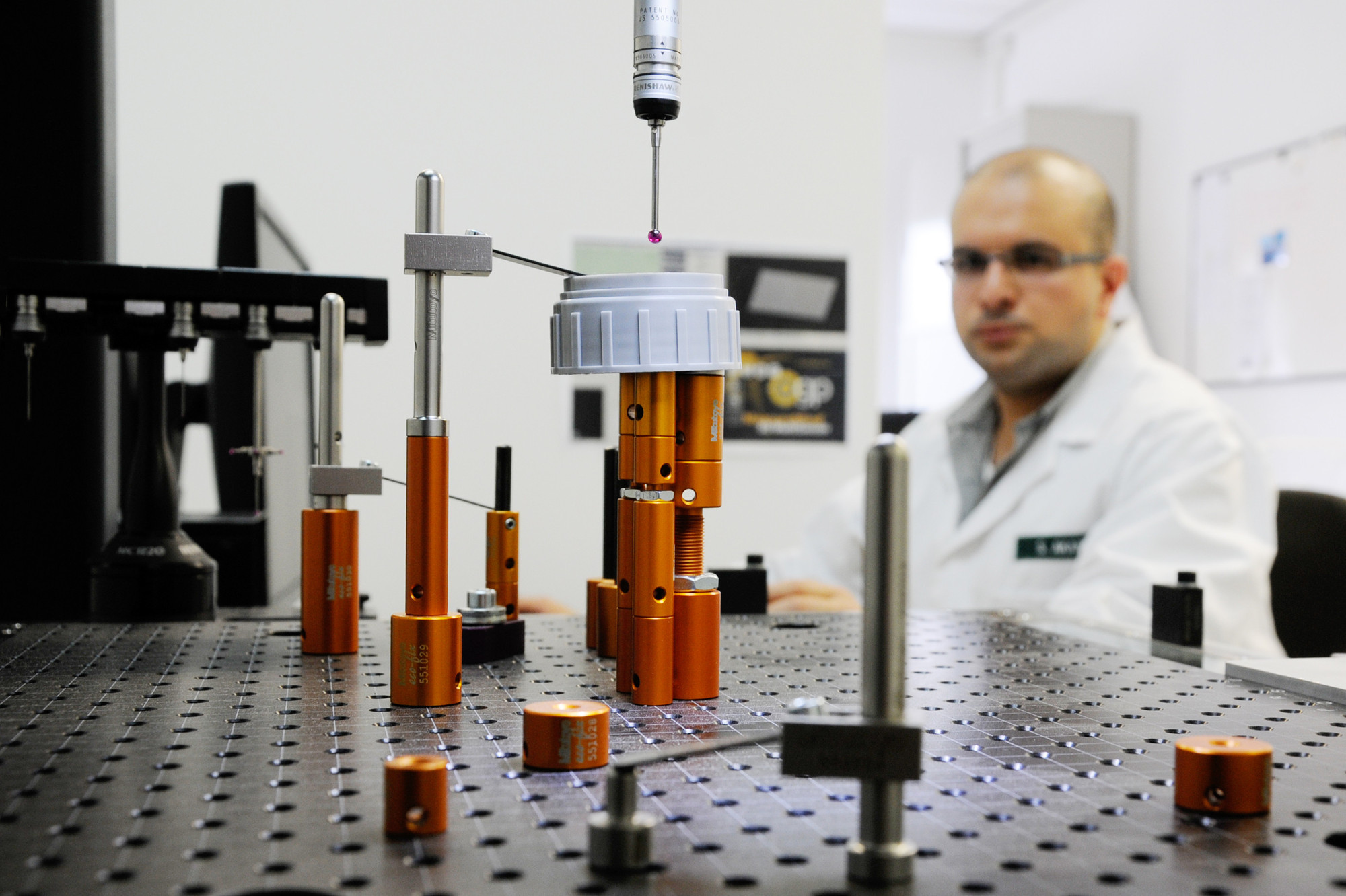
- We turn defined customer requests into describable and quantifiable requirements for the individual divisions of our company.
- Our actions are based on the compliance with the statutory provisions, the standards, laws, regulations and guidelines that are applicable to our company.
- We use preventative quality management tools to help us prevent errors during the design and construction phase among other things.
- Permanent quality improvements achieve a cost reduction and an improved process performance.
- Our employees’ know-how is the basis for the quality of our products and services. Highly skilled, trained and motivated employees with extensive quality, safety and environmental awareness are the focus of the organizational development.
- Suppliers are included in the quality-related, environmental and occupational safety.
Process validation
We carry out the system qualification, process and product validation in accordance with the EU guide to Good Manufacturing Practice (GMP), Annex 15, using the sub-areas IQ (Installation Qualification), OQ (Operational Qualification), PQ (Performance Qualification) and DoE (Design of Experiments).
Additional validation procedures:
- Dosimetric validation in accordance with the DIN EN ISO 11137 standards. Conducted by external service providers.
- Microbiological validation in accordance with the DIN EN ISO 11137-2 standards. Conducted by external service providers.
- Shelf Life (Accelerated Aging Test) in accordance with the ASTM F1980-07 standards. Conducted by external service providers.
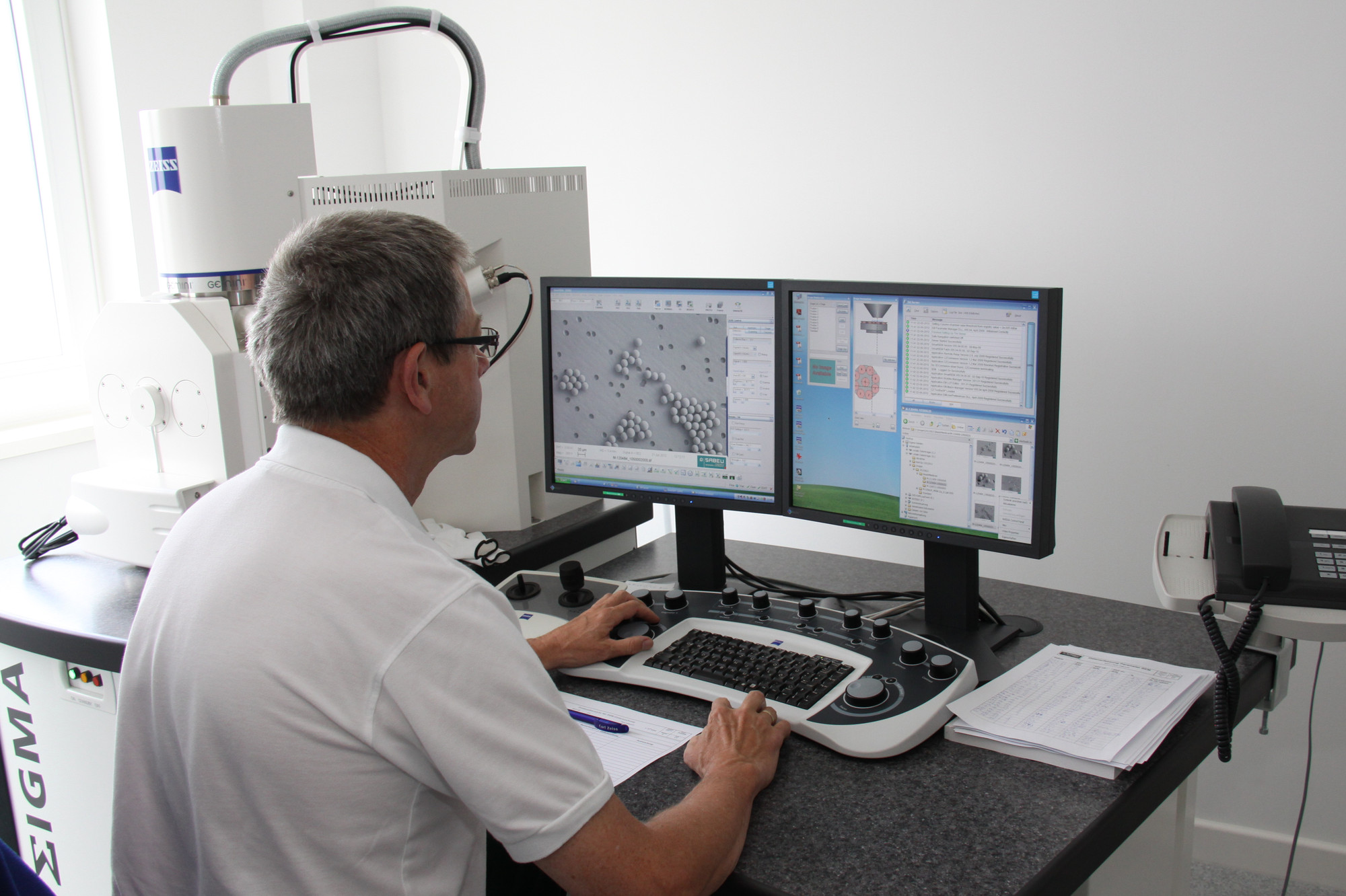
Product validation

We plan and implement validation protocols in consultation with the customers. First sample reports (PPA report – Production Process and Product Approval Report) as set forth in VDA [German Association of the Automotive Industry] Volume 2, Chapter 4 are compiled in order to assess the development states during the development process of the items.
The scope of all validation procedures is described in the validation schedules and can be specifically adjusted and prepared as needed to meet the customer’s needs.
Tests:
- First sample test reports
- Release tests
- Statistical process tests
- Multi-layer process analyses
Test methods:
- Dimensional accuracy tests
- Optical and tactile measurements
- Surface laser scan
- Tension and pressure tests
- Performance tests
- Water Entry Pressure (WEP) tests
- Air flow rate
- Bursting pressure tests
- Leak tests
- Drop test (ADR accordance)
- Differential pressure tests
Good Manufacturing Practice (GMP)
Work hygiene is an essential component of our production process – especially in clean rooms. The effectiveness of the hygiene requirements is monitored and documented with regular controls of the particle count in the ambient air and microbiological analyses in accordance with GMP guidelines.
Our hygiene monitoring includes the regular surveillance of the manufacturing conditions in accordance with the EC guide to Good Manufacturing Practice (GMP) by:
- Counting airborne particles
- Collecting airborne pathogens
- Performing contact tests of surfaces and people
The samples are analyzed by certified accredited laboratories.
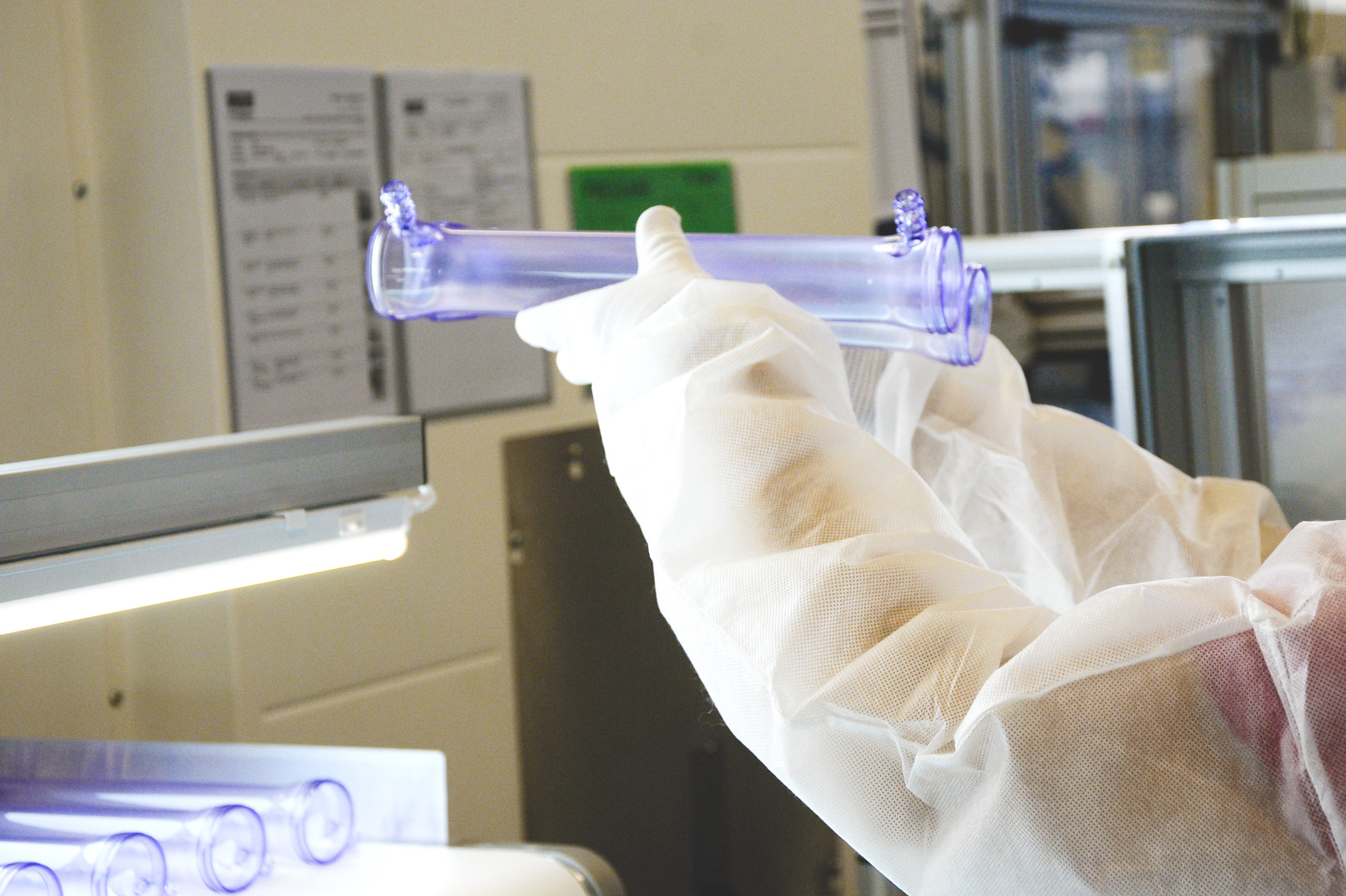